Is Your Design Fit for Purpose?
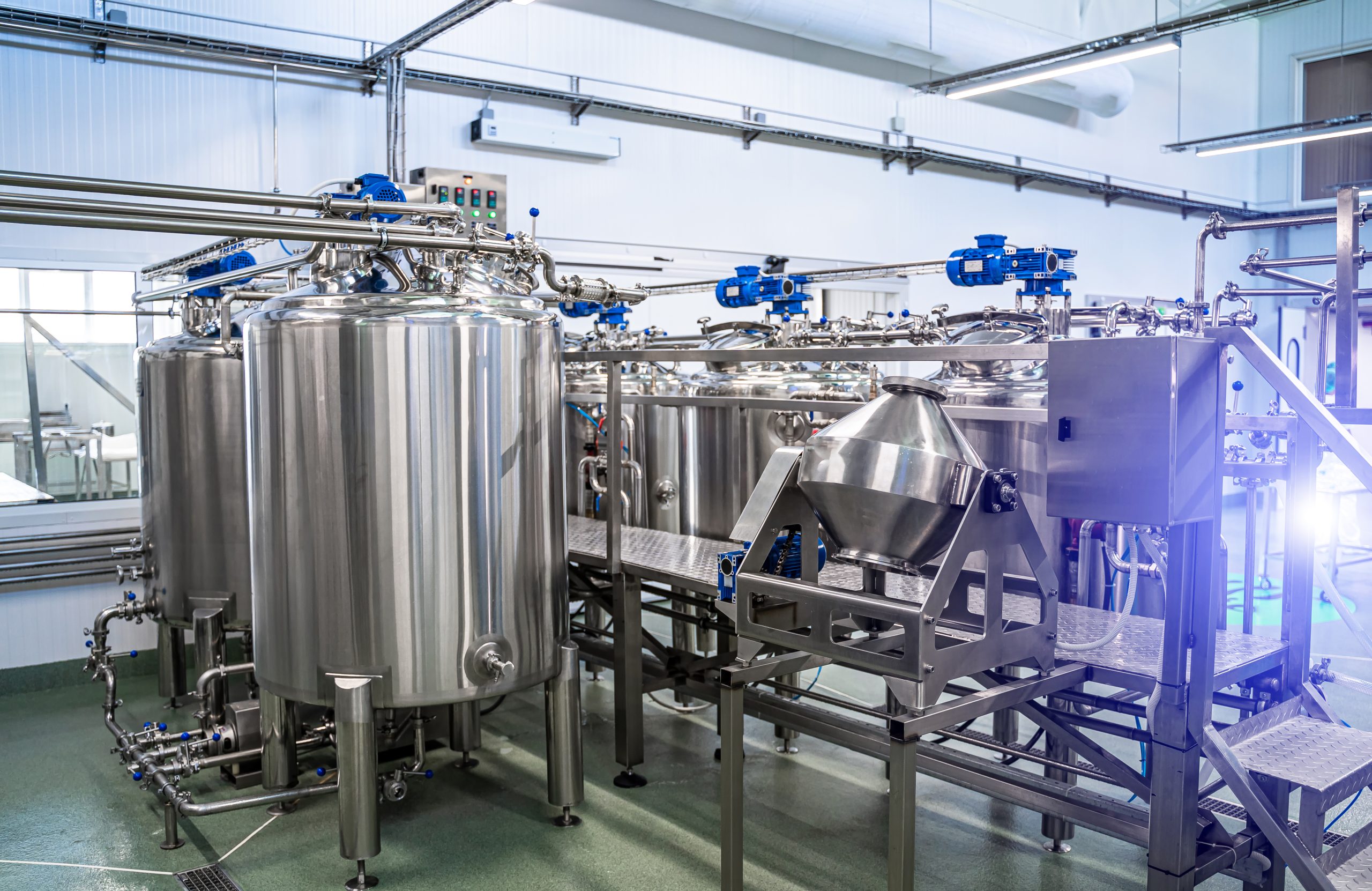
We’ve previously outlined the four steps of any successful design process:
Step 1. Understand the problem
Step 2. Design (plan)
Step 3. Do (Create)
Step 4. Test (evaluate/refine)
In our recent article, we explored Step 1 – Understanding the problem.
Now, let’s cover the next steps 2-4.
After the problem is thoroughly understood and all possibilities and outcomes explored (i.e. the big picture), the design process can begin.
Step 2. Design (the plan)
The most efficient and effective design must be fit for purpose and therefore must consider;
- Manufacture and installation
- The fabrication technique
- Available materials
- Time and resources
- Usability
- Suitability
Manufacture & Installation
The best design in the world is absolutely redundant if it is not fit for purpose. Imagine if a spanner can’t reach a nut in the equipment or if the finished construction is too large to be shipped/craned to the site.
In the factory design process, the considerations for manufacture and installation are pivotal. Manufacturers need to ensure that the layout and design of the factory floor facilitate efficient production processes. This involves optimising the flow of materials and resources to minimise bottlenecks and maximise productivity. Additionally, the machinery and equipment chosen for the factory must be compatible with the layout and be easily installable within the space provided.
Whether it’s arranging assembly lines or installing heavy machinery, meticulous planning is essential to streamlining the manufacturing and installation processes.
In short – designing processes that ensure compatibility between components and systems simplifies installation and greatly reduces errors.
The Fabrication Technique
The choice of fabrication technique directly impacts the design of the factory. Different manufacturing processes require specific layouts and equipment configurations. For instance, factories utilising mass production techniques might necessitate assembly lines with conveyor belts, while those employing custom fabrication methods might require flexible workstations and versatile machinery setups. Understanding the fabrication technique is crucial for designing a factory that can accommodate the production requirements efficiently while ensuring product quality and consistency.
Depth of experience in identifying the correct technique to ensure safety and functionality from an engineering perspective is critical when choosing your Factory Design partner.
Additionally, the techniques familiar to, and utilised by, the available fabricators, especially in remote areas, must be a key consideration.
For example, a concrete bridge may be designed, it may be 100% technically correct, it may be perfect for the conditions BUT, if the only available bridge fabricator or manufacturer available or already contracted only uses steel girders, the design will be redundant.
Available materials, tools and ancillary equipment
The selection of materials influences both the construction of the factory itself and the manufacturing processes within it. Designers must consider the durability, cost-effectiveness, and sustainability of materials to create a functional and efficient facility. From structural elements like steel beams and concrete floors to specialised surfaces resistant to chemical corrosion or high temperatures, choosing the right materials is essential for creating a safe and productive working environment.
And all the while The Goldilocks principle must be considered. Materials must be neither too cheap i.e. low quality, prone to issues, high maintenance costs or too expensive i.e. prone to blowing the budget.
The materials used in the design must be “just right”.
Time and Resources
Efficient allocation of time and resources is paramount in factory design. Delays in construction or installation can have significant ramifications on production schedules and profitability. Therefore, meticulous planning, scheduling, and resource management are critical to ensuring that the factory is operational within the specified timeframe and budget constraints.
Do time and resources allow for a purpose-built option or does the design need to incorporate a measure of generic options to facilitate the project’s resourcing constraints?
Sometimes quantity and/or quality must be tempered to meet a pressing time demand. Alternatively, a staged model may be considered to ensure that the design stages and elements are prioritised in line with time constraints.
Usability
Usability encompasses the ergonomic design of the factory layout, ensuring that it is conducive to efficient workflow and employee safety. Factors such as aisle width, workstation height, and equipment accessibility play crucial roles in usability.
A well-designed factory prioritises ergonomics to enhance worker productivity, reduce fatigue, and minimise the risk of accidents or injuries. Additionally, usability considerations extend to maintenance accessibility, ensuring that machinery and infrastructure can be easily serviced or upgraded without disrupting operations.
By prioritising usability in factory design, manufacturers can create a safer, more efficient, and employee-friendly work environment.
Suitability
In addition to the client scope and goals, there are other factors and considerations of every factory design process in relation to the design’s suitability:
- Who will be using the finished project – do they need additional skillsets? Will the overall design suit the staff affected?
- How does the design fit into the grand scheme and flow of the existing site or with other components of a new or existing site?
- How will the service and maintenance be achieved?
- How will the equipment ultimately be decommissioned and/or removed at the end of its life?
Although a relatively simple concept – Fit for Purpose design – is a very complex practice and one that benefits from experience and innovation in Factory Design Engineering.
For example: A component of the design project was to set out buildings on a site given a generic layout.
Strictly speaking, if we’d designed the buildings 16 m apart, the fire construction codes would have been legally and correctly followed.
However, when forensic, probing and detailed questions were asked at the start of the project, we uncovered a range of products that will be stored and utilised within the buildings that required additional design considerations.
In this example, because we knew what was to be IN the buildings, the buildings were designed 18m apart, to satisfy additional fire and safety regulations.
Imagine if the design consultants in this case weren’t as experienced as those at CDE. Imagine if the buildings were constructed only 16M apart only to have to be removed or significantly modified at a later date, at vast expense?
The ensuing design and construction headaches would be the very least of the factory owners problems!
Experience and expertise always pay dividends.
Step 3 – Create
Both the design, and particularly the creation phase must involve deep consultation with the client.
These final two steps; 3 and 4, are inextricably linked and will often form their own design loop in any project.
Designing, by nature, is an iterative and collaborative process where communication as well as digital and modelling tools are critical.
The entire process must be collaborative – nothing is designed in a vacuum. The client may have regular check-ins over the design process or may be involved during every step of the process
Communication and presentations utilise modalities such as:
- 3D printed or manual design models
- 3D scans for live, real-time changes and tweaks
- 2D drawings for fabrication and collaboration
- 3D picture formats or computer modelling outputs
- Videos and fly-throughs will offer those less technically involved, none-the-less critical stakeholders such as executives and financial stakeholders a view of the entire project before construction
Step 4 – Test
Testing, also known as evaluation and refinement, requires input from all parties involved in the design, installation and manufacturing stage of the project.
There may be many iterations to the design before the project construction is commenced.
During this testing phase, it may be necessary to visit some or many components of the previous three steps before the final design is signed off, ready for the next phases of construction.
Conclusion
Whilst the steps 2-4 above and the previously discussed step 1 are common to all design projects, it is the investment in quality design as part of the Value Engineering principle that will ensure maximum efficiency and efficacy of your entire project.
When you invest in quality design, you save in all subsequent stages of your project. Savings to the bottom-line costs include time, money, stress, efficiency and materials.
Whether you are looking for CDE Design Solutions to work as your engineering team or WITH your internal engineering team, you are assured that all 4 essential steps in the design process are treated as if your project were our own.